Mélange Lindor KONTI
When to choose batch mixing and when to choose continuous mixing? What are the advantages and disadvantages?
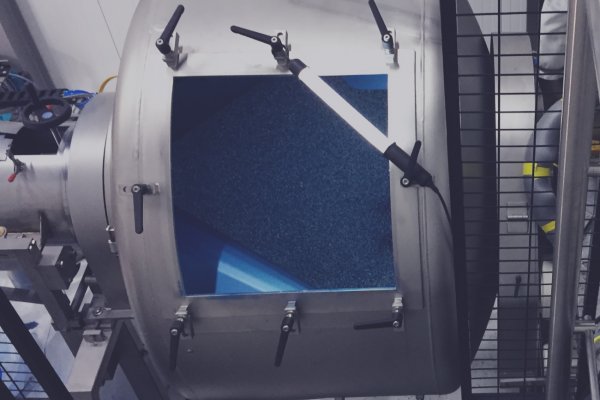
Continuous mixing
Mixing can be done either per batch or continuously. Mixing a ‘batch’ means that a measured quantity is mixed, followed by the next measured quantity that is sent through the mixer. A specific quantity (batch) is used each time to fill and then empty the mixer.
With ‘continuous’ mixing, the required composition of the ingredients is processed by the mixer without starting and stopping. There are no separate steps for filling, mixing and emptying the mixer. With continuous mixing, the mixer is filled and emptied continuously.
When to choose continuous mixing?
By far the most powder mixing processes are batch processes. Continuous mixing can be more advantageous, depending on the application and the circumstances.
Production capacity
With an equal mixing volume in the mixer, more can be mixed per hour with continuous mixing than with the batch process. The reason is, that filling and emptying the mixer does not take up any additional time. Example: a batch of 500. Assuming it takes 1 minute to fill the mixer, 3 minutes to mix and 2 minutes to empty. A total of 6 minutes for 500 kg: 5000 kg per hour. With continuous mixing under equivalent conditions, 500 kg of mixed product is released from the mixer every 3 minutes: 10.000 kg per hour!
Preparing the mixture
Before mixing a batch, the individual ingredients must first be weighed. This also applies to a continuous process, however, this weighing happens continuously. Dosing equipment must ensure second by second that the ingredients being added to the mixer are in their correct proportions. These ‘upstream’ systems usually require a higher investment than for batch mixing.
Changing the recipe
With batch mixing, the recipe can be changed per batch. Apart from cleaning, each batch can be different. With continuous mixing, adjusting the process until it is stable can take a while. It is possible that when starting up, the first few kilos are not to specification.
Continuous mixing is suitable for processes that run continuously for a long time, but is less suitable when variation and flexibility are required.
Tracking & tracing vs. disruption
An advantage of batch processing is that everything is defined per batch: exact composition, process parameters, time. This is more difficult with continuous processing. Tracking & tracing is easier to organise with batch mixing. On the other hand, with every batch there is some risk, however low, of disruptions such as human error or malfunctioning equipment. In a continuous process, everything continues without interruption: there are fewer possibilities for disruptions.
Figure: The choice for batch or continuous mixing depends on production volume and variability of recipes
Plug flow and average residence time
There are continuous mixing processes in which each particle remains in the mixer for almost the same amount of time. The particles that enter the mixer at the same time are mixed only with each other, not with particles that come before or after. This is called a plug flow. Other mixing processes operate with an average residence time, that is, some particles remain in the mixer a little longer and others a little shorter. By slightly extending the average residence time setting, the particles remain in the mixer long enough for a homogeneous mixture to be achieved. Lindor can supply both of these processes. In practice, the average residence time process is used.
Lindor KONTI mixers
Lindor KONTI mixers are fitted with a special metering valve in the outlet that is operated by a servo system. This regulates the outflow. It is essential is that the ingredient supply is of the correct composition at the inlet. This can be designed and supplied by Lindor.
Lindor KONTI mixers from 500 litres (L500 KONTI) up to 25000 litres (L25000 KONTI) can be supplied for a wide range of uses.
Figure: Lindor testing setup for a continuous trial with customer (Lindor Test Centre)
Applications: from plastics to fertilizers to battery powders
Lindor KONTI mixing systems are used for continuously (examples):
- Powder coating sticky plastic pellets after extrusion
- Adding dyes and additives to polymers prior to extrusion
- Coating fertilizer pellets
- Drying and crystallization of super-absorption powders for nappies, among other products
- Cooling and homogenization of battery powders
These and other applications have been and are being tested in trial setups at our test centre, after which the installation is then designed and built.