Lindor verbetert poederstroom in mengproces door innovatie
For over three decades, Lindor has been manufacturing industrial mixers and processing machines for powders, granulates and bulk solids. Among the large variety of applications our powder blenders have been built for, there are a few exceptional powders that tend to cause a fuss.
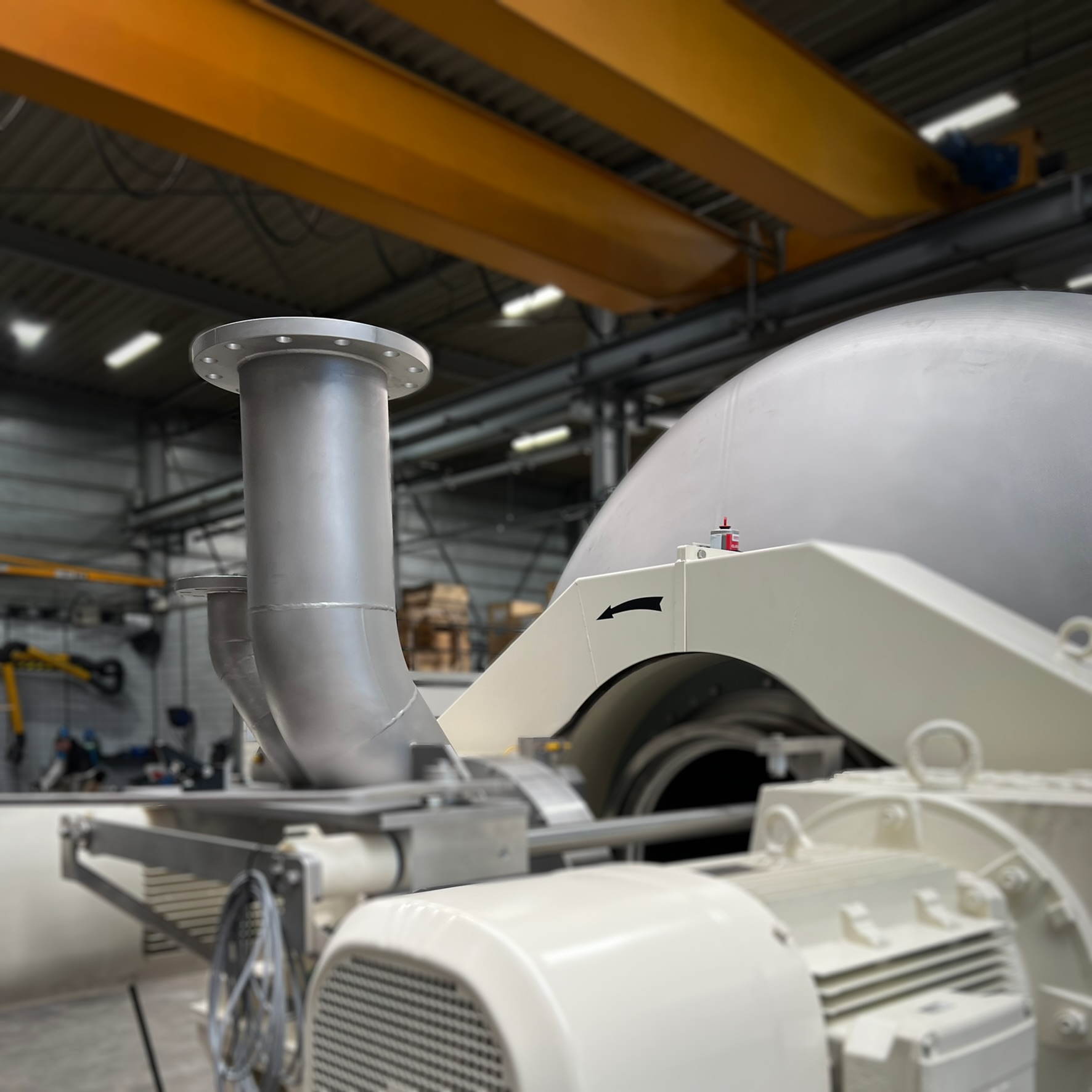
Due to the extremely cohesive properties of very specific types of powders, a challenge can arise in getting these powders to flow from one section of a machine into the next.
We like to refer to them as ‘sticky powders’, and these exceptional powders include:
- Battery powder
- Fine minerals
- Fine ceramics
- Pigments
After having experienced a challenge in the powder flow from the inlet to the drum of our mixer machine, we decided to come up with an innovative improvement for these very special powders.
Flowability of powder is determined by physical properties
The flow properties of powder are determined by the friction between the surface of which the powder needs to slide on (wall friction) and the powder.
Friction is a function of the following powder characteristics:
- Weight (bulk density)
- Particle size distribution (granularity)
Combined with the surface characteristics:
- Surface roughness
- Surface tension
The other important factor is the cohesion of the powder, identified with the ‘angle of repose’. The angle of repose is the angle between a heap of powder and the plane on which it is discharged. Easy-flowing powders, like sugar or silica have what can be described as a very flat heap. This means they have a low angle of repose- typically less than 35°.
More cohesive powders, such as starch or talc powder, have a higher angle of repose. The higher the angle of repose, the taller the heap and more resistant to flow.
Tackling flowability challenge with a design adjustment
For almost all powders, a special coating like Teflon within Lindor powder mixers, along with the water blasting and mirror polishing, is more than sufficient in creating a smooth enough surface for powders to flow over. But for the processing of exceptional powders, a special design adjustment to our standard mixer has been made. In a first step, the angle of the Lindor mixer’s inlet has been adjusted.
Taking the industrial mixer machines within the range of the Lindor L3000-L25000 (maximum batch capacity of 3,000 liters to 25,000 liters) as an example, the standard inlet angle of 45° has been increased to 60° for this machine to accommodate poorly flowing powders. A steeper slope reduces friction and provides more gravity for powders to roll over.
This single change in design is a major first step in increasing the speed at which the powders can flow and paves way for overall success in combination with the next step of the innovation.
Quick and powerful blast of air stimulates powder flow
The main innovation comes from the addition of a new component integrated in the inlet and outlet of the mixer. This part is called AIRSWEEP®.
Lindor engineers source this part from a local distributor in the Netherlands which provides the same quality guarantee as we do and is trusted by industry giants such as Solvay, Cargil and Nestlé.
So how exactly does this component work to create an optimal powder flowability solution?
The installed AIRSWEEP® system creates a shockwave between the wall of the inlet and the powder. The piston, with a dust-sealing valve attached, is the only moving part. It opens very quickly with a powerful blast of air and immediately closes again with a strong spring. This prevents the powder from falling back into the piston. As a result, the sticky powder is cleanly lifted and thus “swept” from the wall, so it can cascade down into the mixing drum.
An ideal powder flowability solution
The combination of these two innovations together- the sharper angle of the inlet and addition of the AIRSWEEP ® system- are a big leap forward in the ability to carry out the gentle mixing of troublesome powders. Further saving you from any possibility of lost production time and ultimately money from production failure, bottlenecks, or the interruptions of having to manually stimulate the powders to flow into the machine.
Furthermore, the AIRSWEEP ® system does not prevent the inclusion of any additional features added to our mixing technology, such as liquid injection, drying, cooling, etc., as these functions are carried out within the drum.
Reach out to us for powder processing solutions
As experts in powder processing and mixing, we can surely advise on your production challenges and custom design the perfect machine to scale your production efficiency.
Learn more about our unique gentle mixing technology here and feel free to contact us via email at mixers@lindor.nl/nl or give us a call at +31-78-6550655.