Lindor Commissions Advanced Coating Mixer for Carbon Fiber Manufacturer
Did you know that Lindor’s rotary drum mixer can be configured with an advanced coating system that makes it an ideal solution for sizing delicate fibers?
This has now been proven in practice, following the successful commissioning of a 1000-liter Lindor coating mixer at a carbon fiber production facility in Europe.
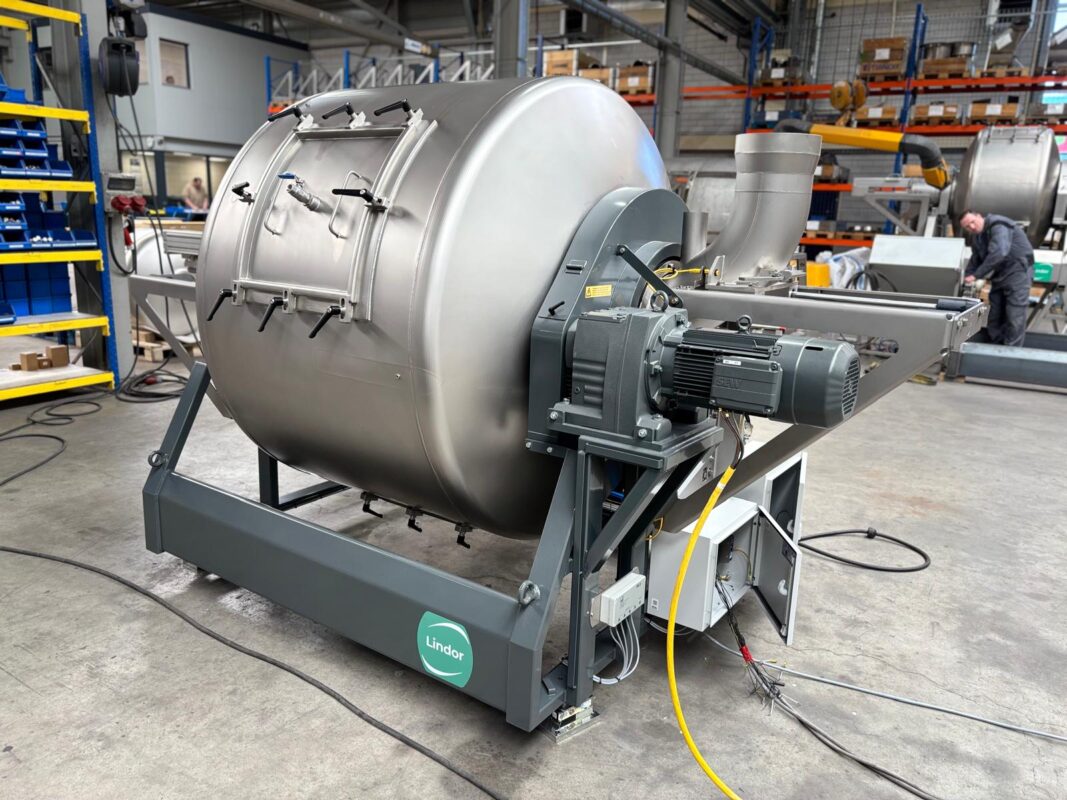
After an in-depth trial at Lindor’s Mixing Test Center in the Netherlands, the carbon fiber manufacturer selected the Lindor rotary drum coating mixer as the optimal solution for their processing line.
The machine is now fully operational at their site and plays an integral role in their carbon fiber sizing process.
This is a critical step in ensuring the fibers bond correctly with composite matrices in end-use applications like aerospace, civic constructions and automotive goods.
Why a rotary drum coating machine is ideal for fiber sizing
In the fiber production industry, applying a sizing layer is essential. Sizing improves handling, protects the fiber during processing, and enhances the adhesion between the fiber and resin in composite materials.
Common methods such as dip baths or kiss rollers are widely used, but each comes with limitations.
This is where Lindor’s rotary drum coating mixer stands out.
Possible Limitations of Alternative Processes |
The Lindor Difference |
Excess liquid retention or waste generation | A precise amount of liquid can be injected into the drum and evenly distributed across all particles |
High risk of fiber damage | Lindor’s gentle touch technology handles the delicate fibers with the utmost care |
Contamination risk | The closed system prevents contamination, and the machine can be further configured with a WIP/CIP system for ultimate cleanliness |
Surface-only coating | Fibers are fully saturated within a short rotational cycle |
Sensitivity to setup | A Lindor machine needs only to be set up once and is very low maintenance |
Limited adaptability | Lindor Engineering can adapt the machine to fit to your processes |
Due to its gentle mixing technology, the Lindor mixer provides a low-shear environment, meaning fibers are neither broken nor compacted. There are no aggressive paddles or fast-moving blades; instead, the fibers tumble in a controlled rotational flow.
Strategically placed spray nozzles inside the drum ensure that the liquid sizing solution is evenly dispersed, avoiding clumping or over-saturation.
The rotational flow in combination with the spray nozzle placement results in an exceptionally homogenous coating across all particles.
Tailor-Made Engineering for a Challenging Product
The carbon fiber manufacturer’s product and process posed several challenges—limited flowability, a high risk of fiber bridging, and regularly changing formulations. Lindor’s engineering team stepped in with a tailor-made solution.
A bespoke liquid injection system was developed to match the client’s frequently changing sizing formulations. The machine was also fine-tuned to prevent product bridging—a common issue with long or fibrous materials that can obstruct flow. With years of experience handling powders, granules, and fragile products, the Lindor team was able to adapt their standard machine design to accommodate this complex product.
“Our client came to us with a challenging material,” said a Lindor engineer involved in the project. “It doesn’t flow well, it’s prone to forming clumps, and their coating recipes vary frequently. But we managed to make it work—flawlessly.”
We Invite You to Test Your Product
Whether you’re processing carbon fibers, glass fibers, aramid, or other chemical products that require precise coating, Lindor’s rotary drum mixer-coater can be configured to meet your needs.
Interested in seeing if a Lindor coating mixer is right for your application?
Contact Lindor today to schedule a test run with your material and experience the benefits of precision coating with a gentle touch.