The Core Benefits of Low-Shear Mixing in Rotary Drums
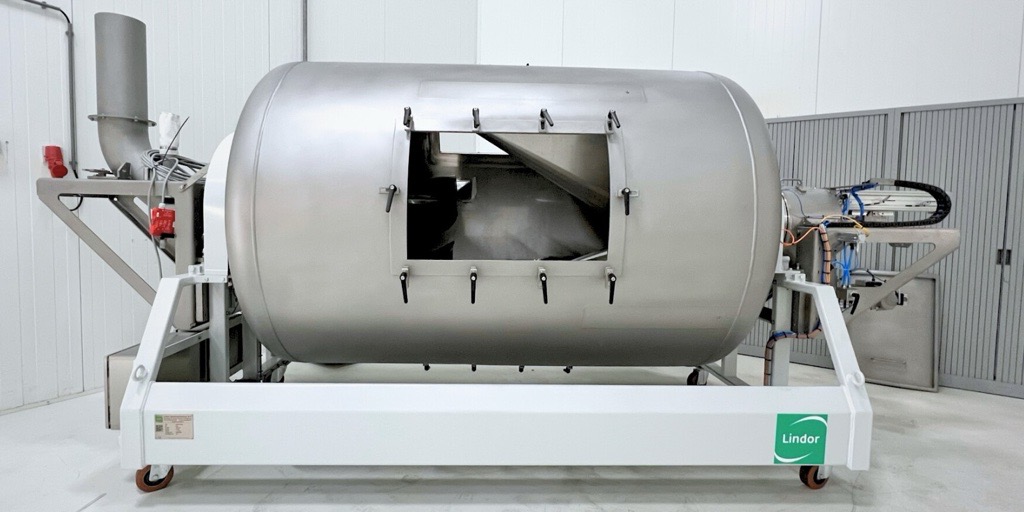
Choosing the right mixing equipment is critical to achieving the best product quality while minimizing waste. When handling very fine, delicate, heat-sensitive, or even dangerous powders and bulk materials, a rotary drum mixer (or rotary drum blender) is often the best option.
This article explains the quality and operating benefits you can expect from integrating a rotary drum mixer into your processing line.
Low-Shear Rotary Drum Mixing
What sets the rotary drum mixer apart from other types of industrial mixers is that it has no moving parts inside the drum. Instead, it uses a process called diffusion mixing. With diffusion mixing, gravity, a stationary blade design, and the drum’s slow rotation are what mix the product.
The materials are lifted by the unmoving mixing blades, cascaded, and tumbled as the drum rotates. This gentle tumbling action helps protect delicate particles and blend the product evenly in a short time.
Rotary drum mixer machines thoroughly blend without creating areas of uneven concentration. In addition, the gentle mixing process minimizes friction, which means very little heat is generated.
The continuous and repetitive motion leads to a consistent, uniform blend across the entire batch volume, which is often challenging to achieve with other low-shear mixers relying on localized agitation.
Learn more about Lindor’s gentle mixing technology here.
Quality Benefits of Rotary Drum Blending
The greatest benefits in terms of quality can be classified as:
- Preservation of particle integrity
- Excellent homogeneity
- Virtually no heat generation
Preservation of Particle Integrity
Preservation of particle integrity not only maintains the quality but also improves the overall yield of the process.
The controlled, gentle mixing action helps keep each particle’s original size, shape, and structure intact. This is essential when dealing with reactive materials or fragile particles that could break apart if mixed too harshly.
By maintaining the physical properties of each particle, the mixer reduces the generation of dust and fines. Therefore, there is no unnecessary loss of ingredients due to breakage. As a result, there is less waste of valuable product and a higher quality batch consistency.
Excellent Homogeneity
The continuous rotation of the drum ensures that every part of the batch is exposed to the mixing action. This even exposure prevents the formation of unmixed zones, which is especially important in industries like food processing and chemical manufacturing.
Consistent flavor, texture, and reactivity can only be achieved if the mix is uniform.
In systems like the Lindor rotary mixer, the gentle tumbling pattern also promotes excellent liquid dosing for applications requiring coating, soaking, or impregnation. The natural flow of material and the strategic location of spray nozzles allow for an even distribution of liquids over the surface of particles.
No Measurable Heat Generation
A further quality benefit is the reduced heat generation during mixing. Since the rotary drum mixer relies on tumbling rather than aggressive mechanical agitation, there is minimal friction. This low friction helps avoid hotspots that can damage heat-sensitive materials.
Without excess heat, the blend stays free-flowing and homogeneous. This means no lumps or clumping, so your ingredients remain undamaged and fully effective while avoiding unnecessary waste.
Operational Benefits of Rotary Drum Mixers
The greatest benefits in terms of operating a drum blender can be classified as:
- Operational efficiency
- Easy cleaning, inspection and maintenance
- Versatility across applications
Operational Efficiency
Challenging some beliefs that diffusion mixing takes a long time, sophisticated rotary drum mixers, such as the Lindor models, mix bulk materials quickly, effectively, and with minimal power usage.
Rotary drum mixers are also particularly well-suited for large-scale, bulk mixing operations. They are able to effectively handle heterogeneous materials, even when particle sizes and bulk densities vary widely.
And because these mixers operate at a lower rotation speed and need less power, they keep energy costs on the lower side. Lower power consumption not only saves money but also supports sustainable manufacturing by reducing the overall energy footprint.
Easy Cleaning, Inspection & Maintenance
Many people think rotary drum mixers are hard to clean, but advanced engineering has solved this problem.
The design of Lindor mixers features a smooth, rounded interior that prevents particles from getting stuck in crevices. Enhanced cleaning features reduce downtime, help maintain the highest standards of hygiene, and make routine inspections and maintenance easier.
The simplicity of cleaning and upkeep is one reason Lindor rotary drum mixers are considered a practical choice for many processing lines.
Versatility Across Applications
Lindor rotary machines have proven to work well in a wide range of applications, including food, nutraceutical, chemical, polymer, and pharmaceutical production. Customization options and their ability to handle different types of materials and large batch sizes makes them an adaptable option in many processing lines.
Discover our Client Success Stories here.
Contact Us Today
By choosing a Lindor rotary drum mixer, you can improve your production process and achieve better results while reducing waste and potentially lowering overall costs. Reach out to our specialized process engineers to find out if a rotary drum blender is a good fit for your product and processing line.