Visit Lindor at POWTECH Show, Nuremberg. Get your free ticket here.
Specially Designed Battery Powder Mixer is added to Lindor’s Product Range
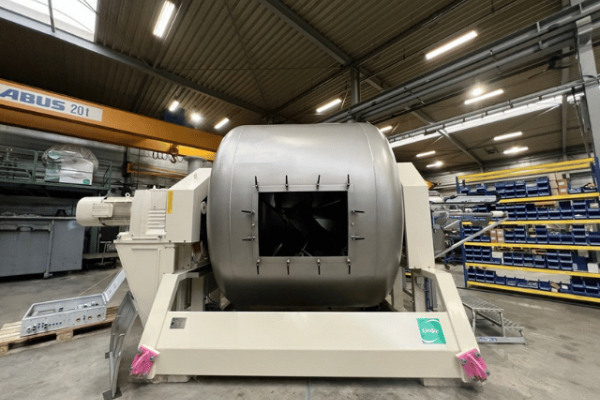
[DORDRECHT, The Netherlands, 15 December 2022] – Lindor sends out a new, state-of-the-art battery powder mixer for delivery to a client in Japan.
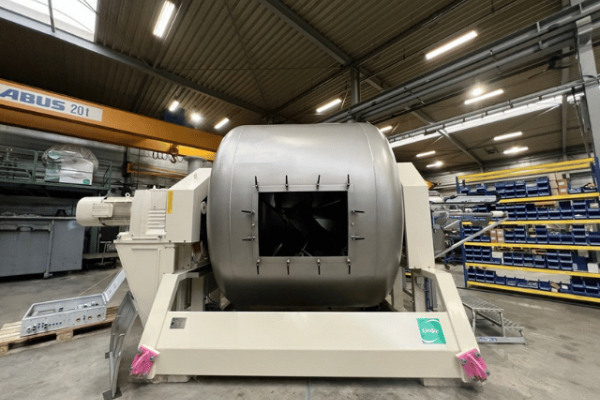
A series of innovations in the powder blending machine design has led to the successful execution of the newest Lindor mixer, specially designed and optimized for battery powder processing.
The demand for battery powder is soaring.
According to Statista, the size of the global lithium-ion battery market is projected to grow by over 72% by 2026, which puts pressure on battery manufacturers to scale production quickly. However, battery powder comes with a unique set of challenges for manufacturers- namely regarding the risk of metal ingress.
Lindor has been engaged in battery powder mixing projects for well over 20 years. The unique gentle touch technology with which Lindor mixers operate is particularly well-suited for powders that are especially sensitive to metal contamination, as there are no moving parts within the mixing drum.
To answer the demand from battery manufacturers to develop brand-new production plants or install additional processing lines with updated, energy efficient machines, Lindor has engineered a novel solution for several mixing, cooling and drying functions.
In realizing the newest battery powder mixer, adaptations had to be made to the Lindor base model mixer.As battery powder is a highly cohesive powder with a high angle of repose, the angle of the inlet has been steepened to allow for better powder flow into the drum of the mixer. The angle of the scoops within the drum has also been steepened as well as mirror polished, to allow the powder to slide off easily as it blends.
Powder flow is further stimulated by an installation of a special component, in both the inlet and outlet of the mixer. The special component consists of a spring and piston that quickly release and close, sending out a powerful shockwave to sweep the powder down into the drum.
While these innovations are enough to allow a Lindor mixer to process almost every other type of powder, the stringent quality requirements for particle shape, size, and purity (i.e., the absence of metal contamination) drove the last details of the innovation. These details include the use of alternative materials to further reduce any risk of metal contamination and special seal constructions tailored to combat the abrasive properties of battery powder.
“Battery powder is a very high-quality product which demands precisely-engineered process equipment,” commented Managing Director Bastiaan Soeteman. “Lindor mixers, coolers, and dryers facilitate quality requirements while operating with optimum production efficiency.”
With an optimized design and high energy efficiency, Lindor’s new gentle touch battery powder mixer serves as an ideal solution for the coming new production lines expected to spring up around the globe.
To learn more about the different solutions our engineers can deliver to your battery powder processing line, reach out to us today.